Navigating the changing landscape of flexible packaging regulations:
A guide for food processing facilities and CPG companies.
In recent years, the landscape of flexible packaging regulations has been rapidly evolving, presenting both challenges and opportunities for consumer packaged goods (CPG) companies and food processing facilities. As the demand for sustainable packaging solutions continues to grow, it’s crucial for industry leaders to stay informed about these changes and understand how they can adapt to meet the evolving regulatory requirements.
Flexible plastics encompass a wide range of packaging materials, including films, pouches, and wraps. These materials offer numerous advantages, such as lightweight, durability, and cost-effectiveness. However, recent regulatory shifts emphasize the importance of sustainability and recyclability in packaging design.
Often used in single-use packaging, flexible plastics have been put under the microscope because of the environmental impact. However, with proper understanding and strategic decision-making, flexible packaging can still play a vital role in the packaging industry while minimizing its ecological footprint.
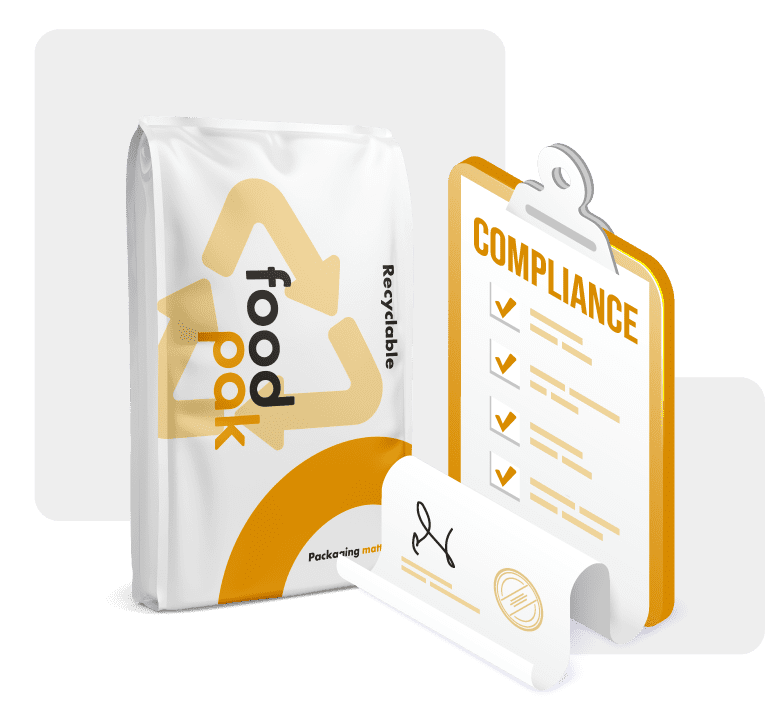
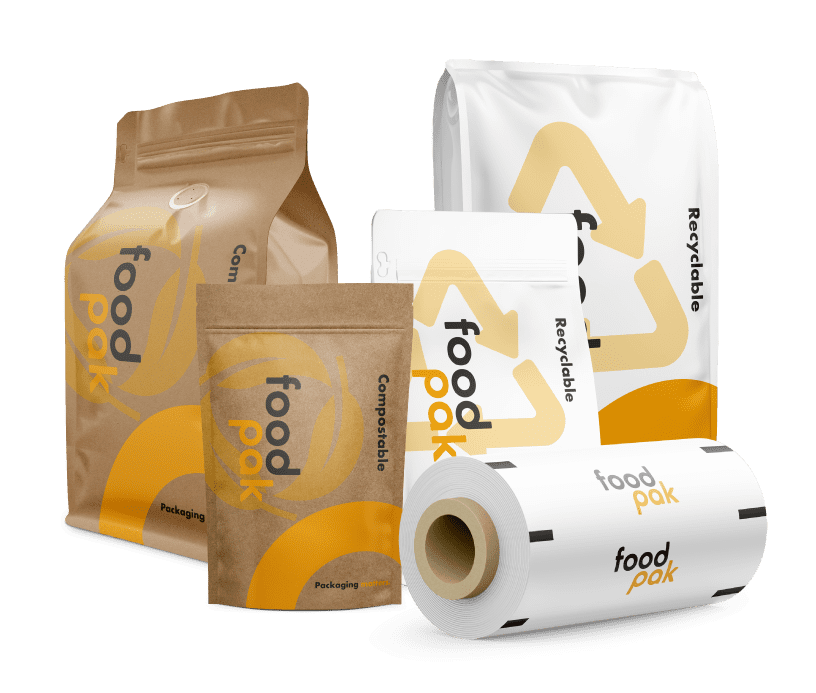
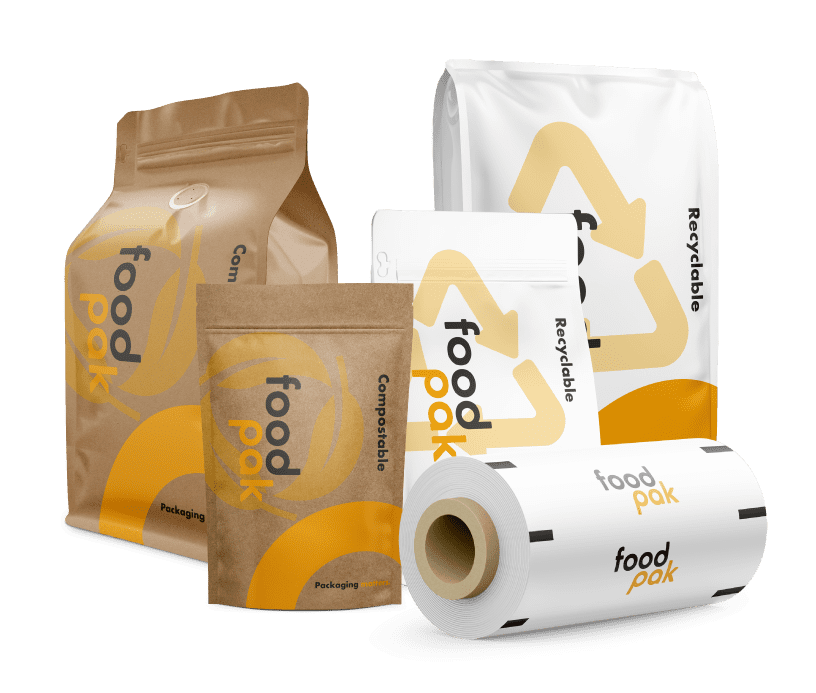
Where are the trends and regulations leading in the next couple of years?
More and more, large retailers are creating more stringent requirements for their vendors using flexible packaging. According to the most recent ESG reports, large retailers like Loblaw and Walmart are looking to have 100% of the plastics in their stores being reusable or recyclable by 2025.
It’s possible that more large retailers will begin to adopt the usage of more sustainable solutions as a requirement, so it’s important to keep this in mind for food producers who are looking to scale up with their distribution or those who have their products in a variety of stores.
To avoid the costs of wasting laminated packaging, it may be worth it for retailers to consider alternatives to their packaging to stay ahead of the curve.
What you need to know about recyclable flexible plastic.
Traditional flexible packaging is made up of laminated films with different types of plastic which need to be delaminated for proper disposal. Since recycling facilities are not equipped for delamination, it isn’t presently possible to recycle standard flexible plastic.
Monostructure packaging, or mono-material packaging, involves using a single type of material for packaging, simplifying the recycling process, and promoting the circular economy.
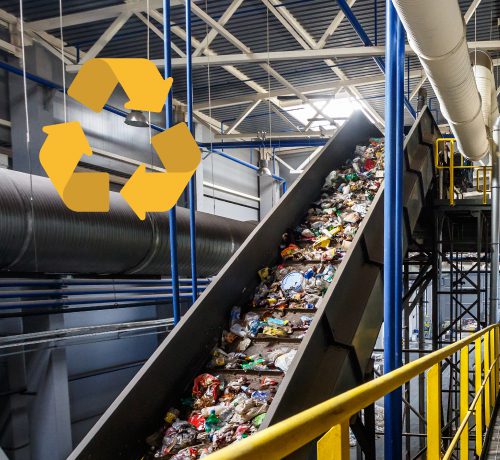
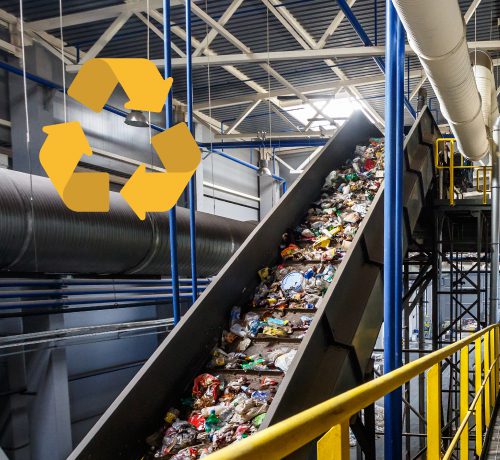
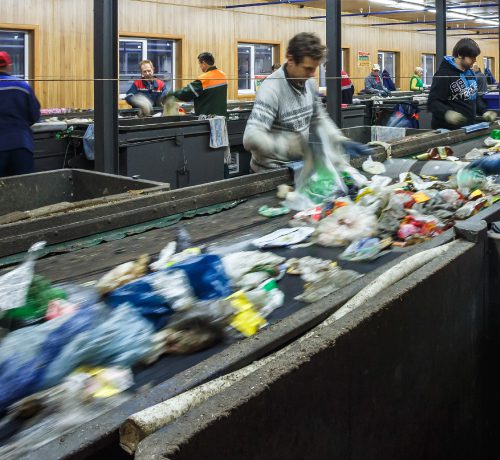
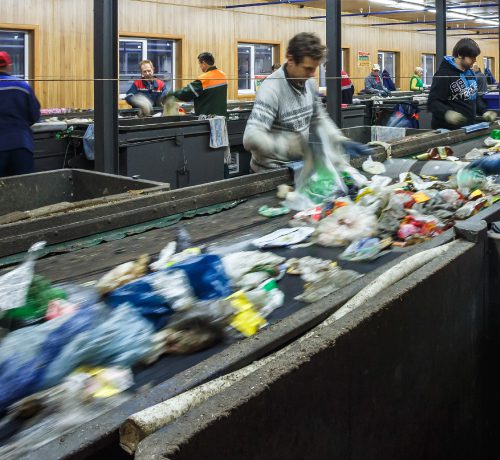
When film is recyclable, typically it’s a monostructure material, meaning the packaging has laminated materials that are made up of the same plastic structure. For a material to be considered recyclable in Canada, >90% of the packaging should be made up of the same material. In that case, packaging doesn’t need to be delaminated before disposal.
Depending on the structure, barrier layers can still be added if 5-10% of the total component weight to help maintain the shelf life of your product.
While transitioning to monostructure packaging may require initial investments and adjustments, there are significant long-term benefits in terms of sustainability and compliance.
Types of monostructure packaging:
There’s a wider variety of monostructure packaging than ever before. While not all types of film have a recyclable option, these are the types of recyclable packaging we offer:
Preformed pouches
Shrink bags
Thermoforming film
Flow wrap film
VFFS film
Key considerations if switching to monostructure packaging:
1. Packaging performance requirements.
Barriers, resistance, strength, and appearance properties can vary between plastic structures. Some products may require high-barrier or puncture resistant structures that may not be readily accessible with monostructure materials.
2. Environmental considerations.
If monostructure packaging can’t offer the same food preservation as traditional packaging, shelf-life may decrease, leading to increased food waste. The end-of-life recyclability should also be considered to make sure consumers are aware of the proper way to dispose of this packaging to prevent recyclable plastics from going to the landfill.
3. Compatibility with existing machines.
Packaging equipment may have different requirements. Before switching to monostructure materials, it would be beneficial to test the film on your machines to avoid the chance of choosing a material that doesn’t work with your machine and prevent interruptions in production.
4. Packaging compliance.
It’s important to evaluate the effectiveness in terms of safety, compliance, logistics, consumer accessibility, convenience, and branding requirements while assessing new packaging suppliers for monostructure materials.
5. Market availability.
It’s worth considering that monostructure materials aren’t available at all suppliers, and minimum orders are typically higher compared to traditional plastics. Securing a stable polymer supply and competitive costs can help to maintain market competitiveness.
Why should you consider using flexible packaging?
Despite the challenges posed by evolving regulations, flexible packaging remains a viable and valuable option for food processing plants and CPG companies.
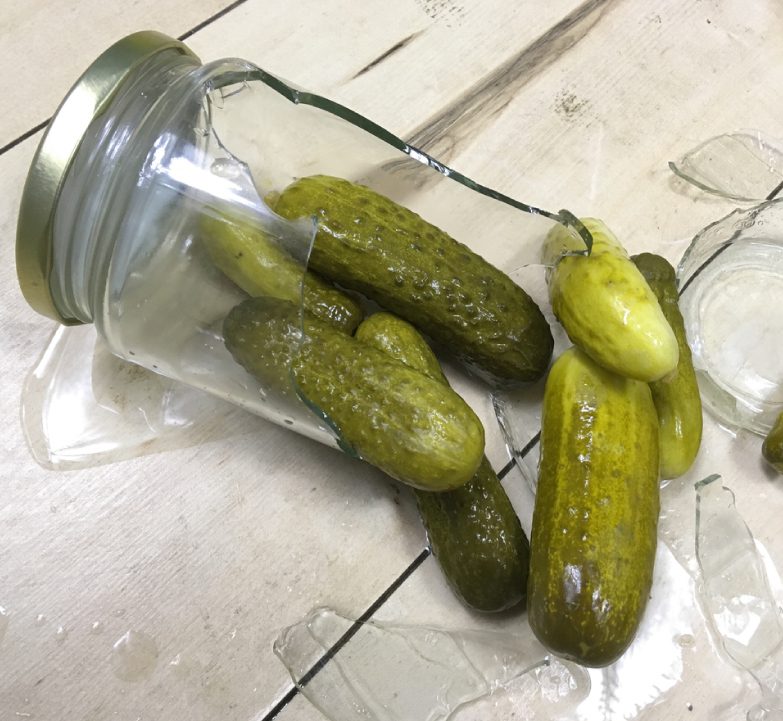
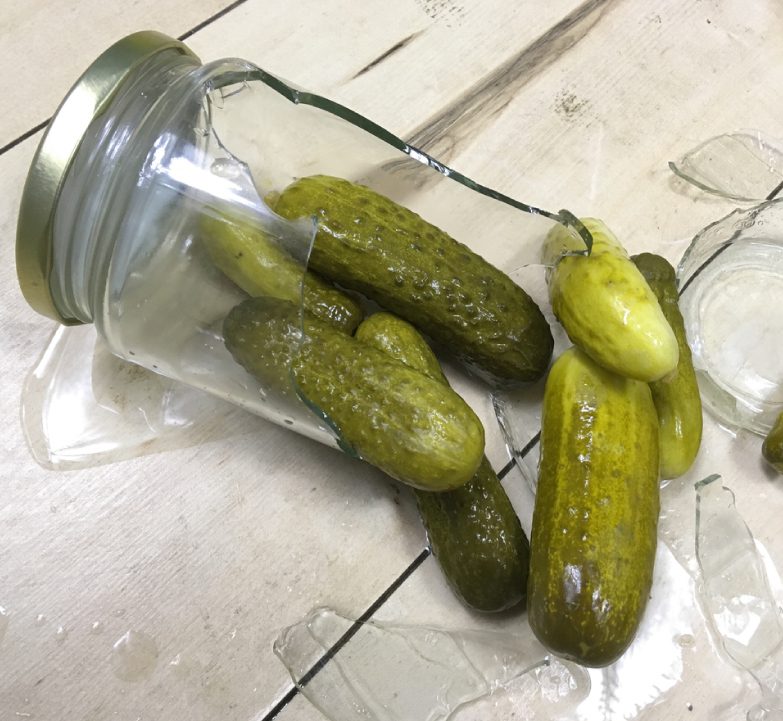
Lightweight and compact. Studies have shown that bulky glass jars can take 26 truck loads to transport the same number of units of flexible plastic packaging that can be transported in one truck. Flexible plastics can greatly reduce fuel usage and transportation emissions through compact shipping and transport, especially in large volumes.
Minimize product waste. In both delivering jars and cans to processors for filling, and in delivery to stores, packaging often arrives damaged. Whether it’s cracked jars or dented cans, it can cause an unnecessary amount of waste and often requires more packaging, like bubble wrap, Styrofoam, or double boxing to prevent breakage.
Minimize product to packaging ratio. Compared to cartons, cans, and glass, flexible pouches have the least amount of packaging to portion the same volume of product. An analysis showed that cartons, cans, and glass use 2.5X, 18X, and 36X more packaging than flexible plastic.
Improve branding with less added material. Flexible packaging also offers flexibility in design by printing directly onto the packaging, utilizing the full area of the packaging and removing the need for labels, stickers, and adhesives on your packaging.
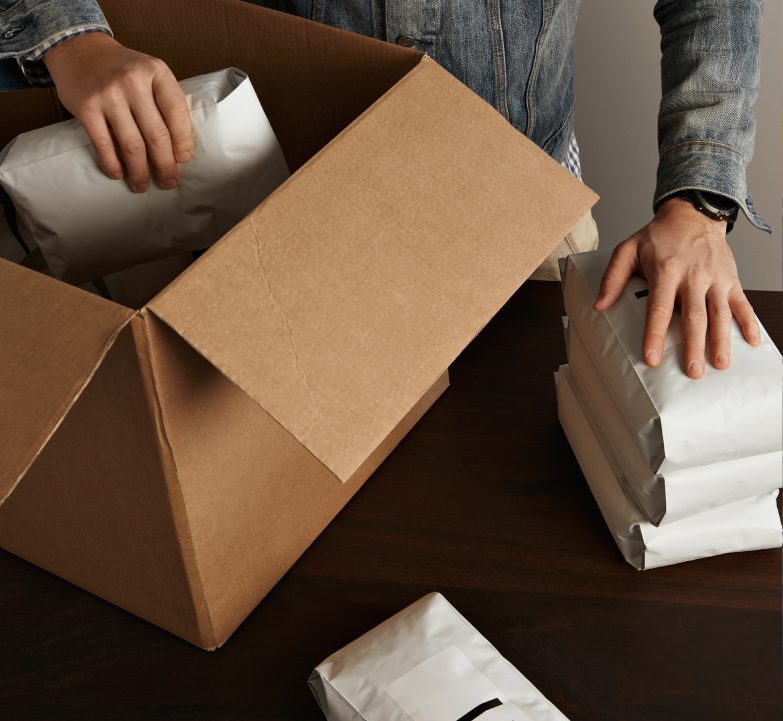
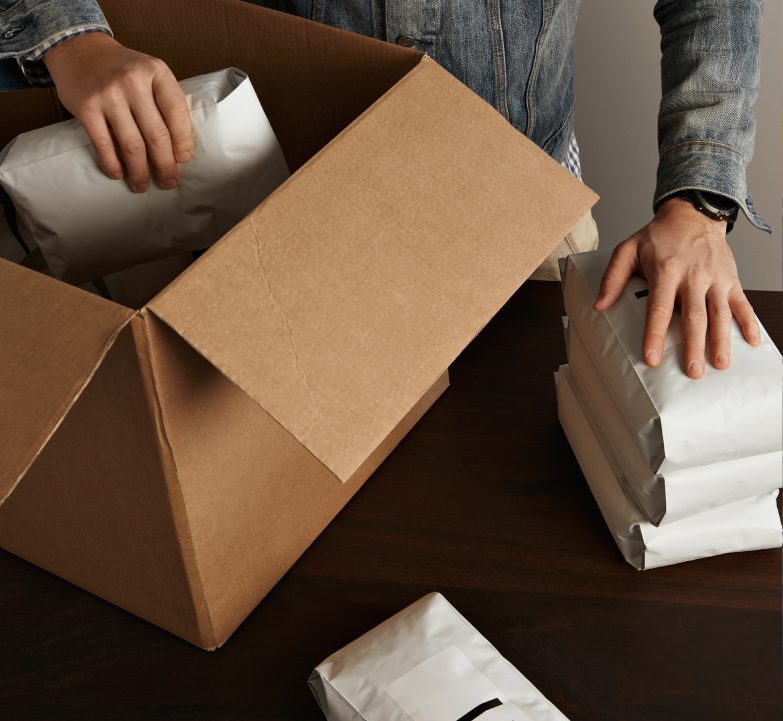
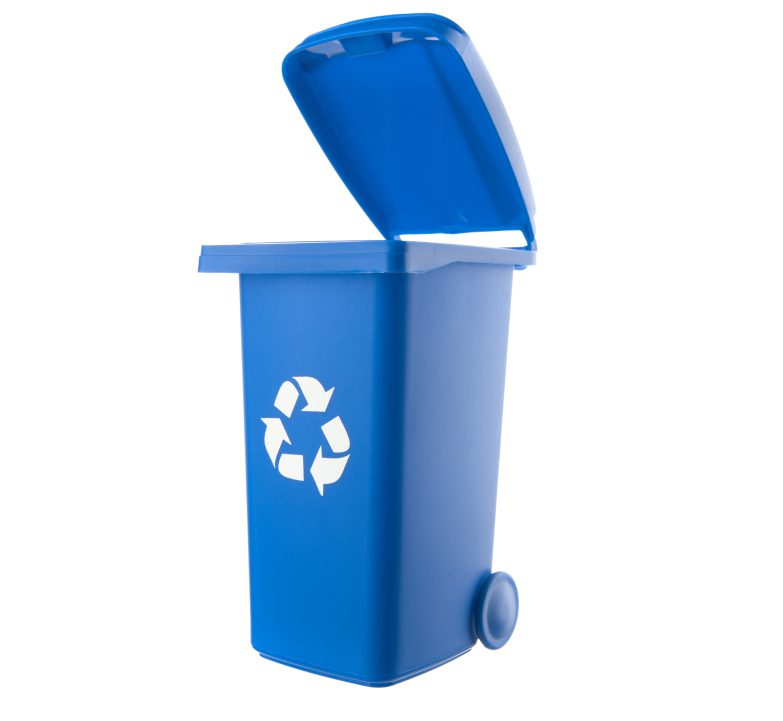
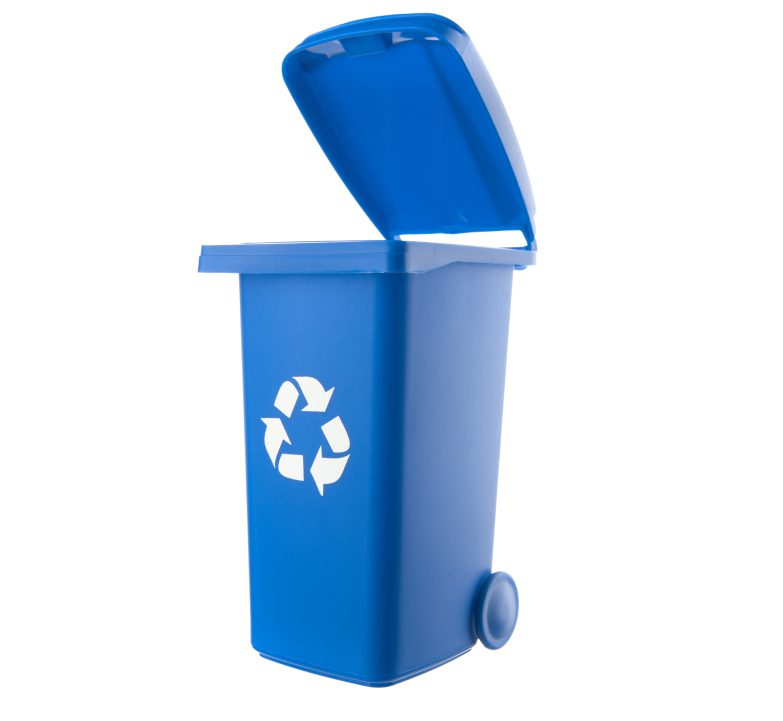
Proper flexible packaging disposal.
The ability to recycle flexible plastic may vary between municipalities. It’s important to educate customers on the proper disposal of packaging depending on their area. Many municipalities in North America have store drop-off or recycling depots that can handle plastic packaging as flexible plastics generally aren’t blue bin recyclable.
Educating consumers on the proper disposal of flexible plastics is essential in promoting responsible waste management practices. Providing clear instructions on recycling or disposing of flexible packaging can help reduce contamination in recycling streams and increase the likelihood of proper disposal.
Wrapping up
Navigating the changing landscape of flexible packaging regulations requires proactive engagement and strategic decision-making from owners of CPG companies and managers of food processing plants. By staying informed, embracing sustainable packaging solutions, and educating consumers, industry leaders can contribute to a more environmentally friendly and socially responsible packaging industry.
Share this post
Have a project in mind?
Get in touch today for a custom quote.