Owning a vacuum sealer.
Vacuum sealers are an essential piece of equipment for food producers and restaurants alike. They help to increase the shelf life of products, keeping them fresh when needed, and aid chefs in recipe development. Like any other machine, vacuum sealers can run into issues that can keep them from working efficiently. Being able to diagnose and troubleshoot simple issues may help you keep your facility running smoothly.
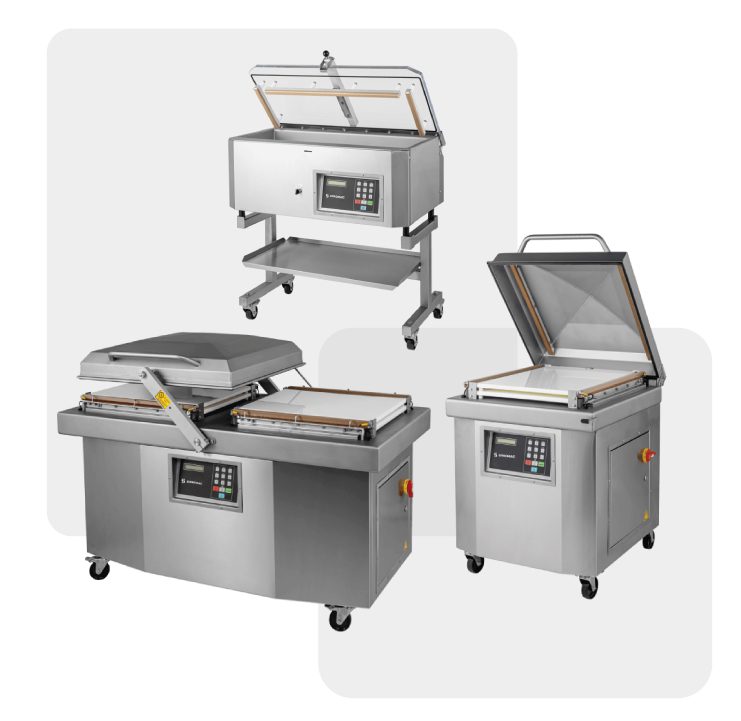
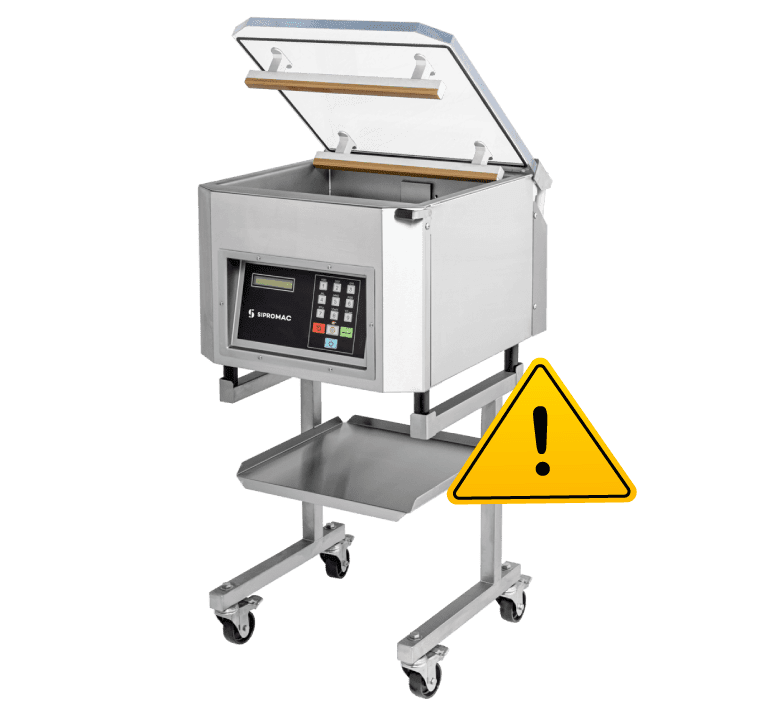
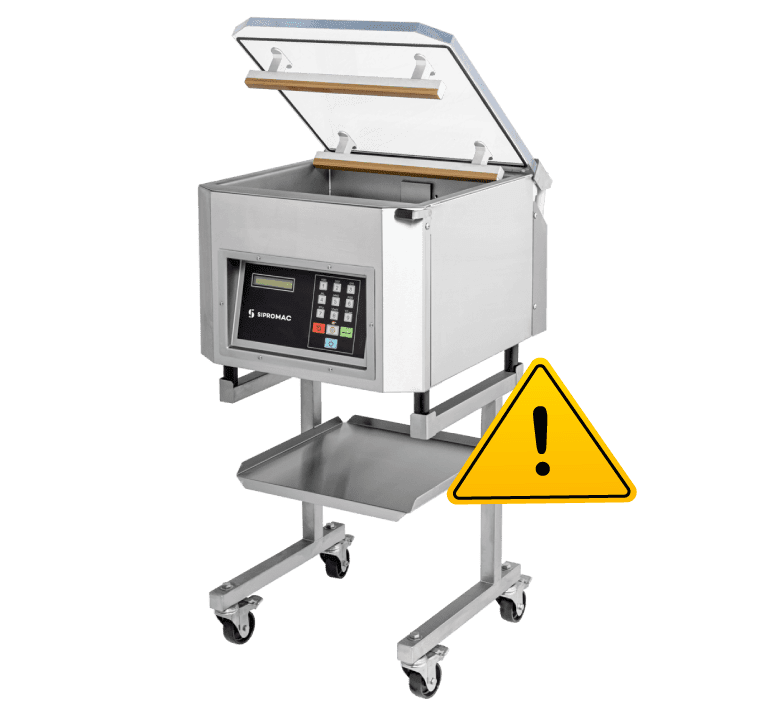
How to troubleshoot common vacuum sealer problems.
1. Machine Isn’t Sealing: One of the most common issues with vacuum sealers is seal failure. This can be caused by a variety of factors, including dirty sealing bars, worn-out seal bar coverings, broken seal elements, and incorrect sealing settings. Check that the sealing bars are clean and free from any debris.
2. Not Enough Vacuum: This can be caused by poor pump performance, air leaks in the chamber, or other issues. Check your machine’s vacuum indicator to see the approximate vacuum performance. Check the lid gaskets and replace any that are damaged or worn-out. Make sure to check the pump hoses for any obvious damage or loose connections. If problems persist, FoodPak technicians have a high-precision digital vacuum gauge which can check in-chamber vacuum performance and test for leaks.
3. Overheating: Overheating can be seen when the bars melt the plastic. This can be caused by running the machine for too long without allowing it to cool down, which can result in a burnt-out heating element or a damaged seal. Allow the machine to cool down before using it again. If the machine overheats excessively or it overheats without excessive use, check that the Teflon tape on the bars is in good condition and make sure the seal time is not too high. Otherwise, there may be another issue within the machine.
4. Poor Sealing: Inadequate sealing can be caused by a variety of factors, including dirty sealing bars, leaky seal bladders, and incorrect sealing settings. Check that the sealing bars are clean and free from any debris. Replace worn-out seal bar coverings, ensure proper seal bar mobility, and adjust the sealing settings to ensure a consistent seal
5. Machine Not Turning On: If your vacuum sealer is not turning on, it could be an issue with the power cord, the power socket, or it could be a blown fuse. Try using the machine on another plug and testing other electronics on the plug if possible. If the socket is not the issue, further investigation of the machine might be necessary.
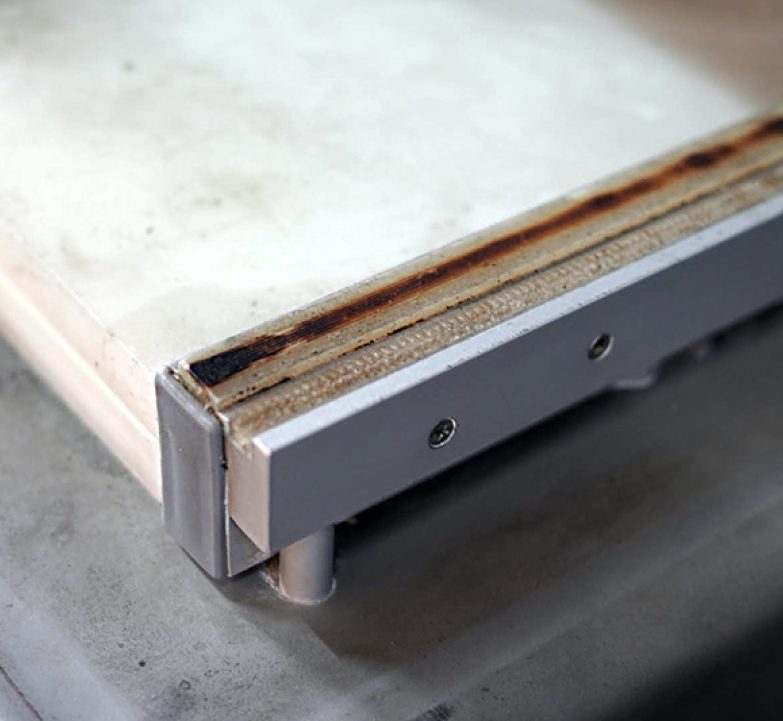
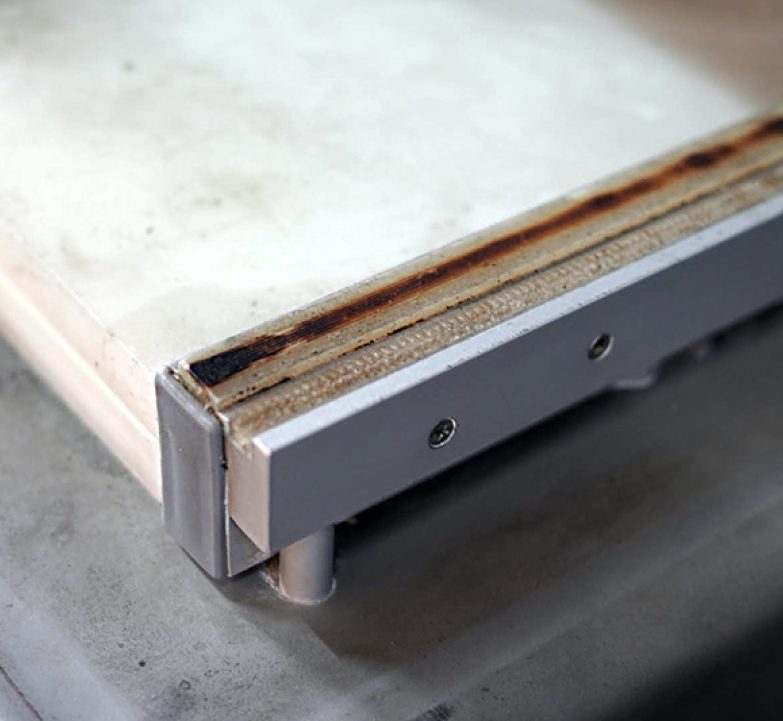
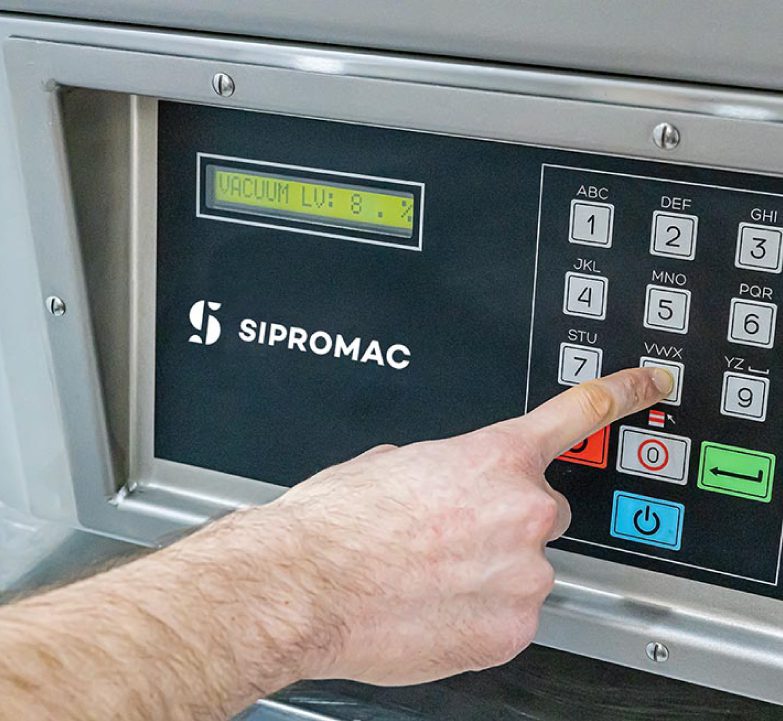
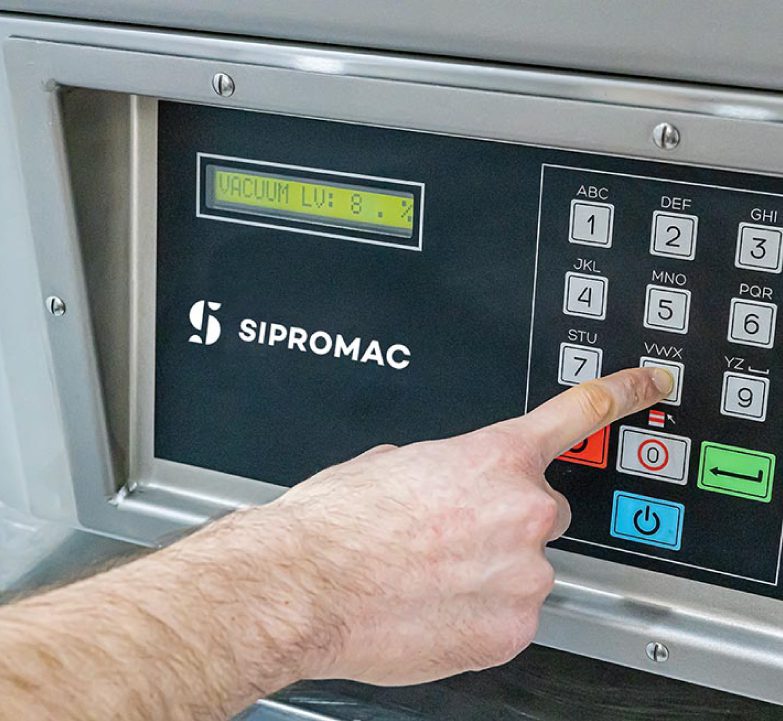
Does your machine have a different issue?
If the problem with your vacuum sealer isn’t clear or if your vacuum sealer needs additional parts for repairs, reach out to our service department to schedule time with one of our specially trained packaging machine technicians. There are a number of issues that come up on a vacuum sealer that can be quickly diagnosed for effective vacuum sealer repairs.
Being able to diagnose and troubleshoot simple issues may help you keep your facility running smoothly.
Preventative maintenance.
One way to prevent breakdowns is to make sure you keep your machine maintenance up to date. It’s recommended to maintain the machine, including actions like changing the oil and the Teflon tape on the bars, every 6 months to prevent issues from arising. Catching smaller repairs early can prevent more challenging and costly issues like a seized pump.
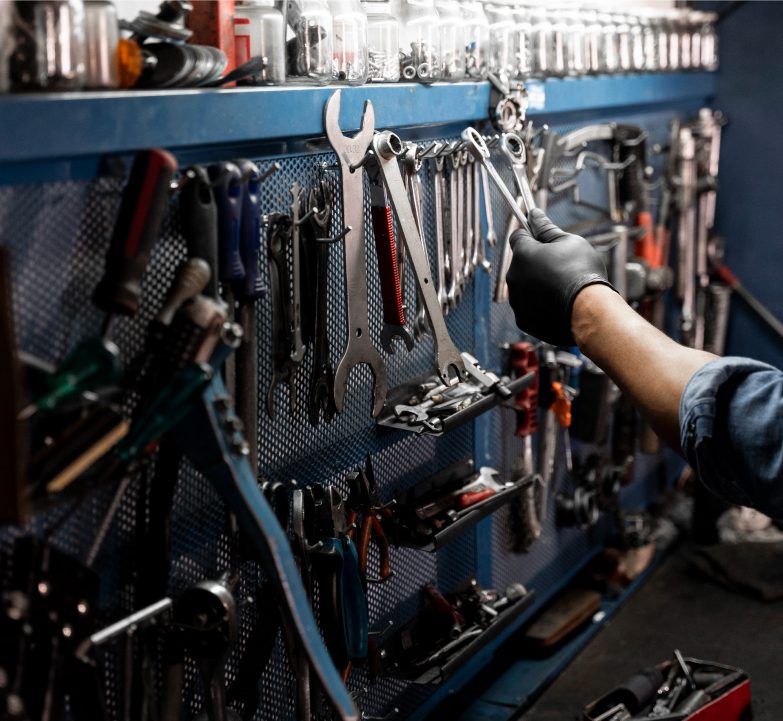
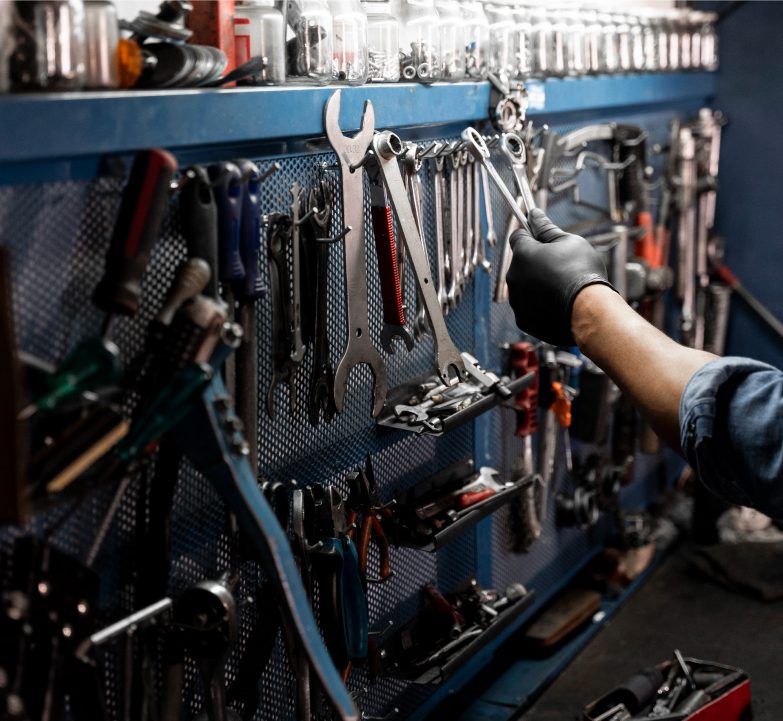
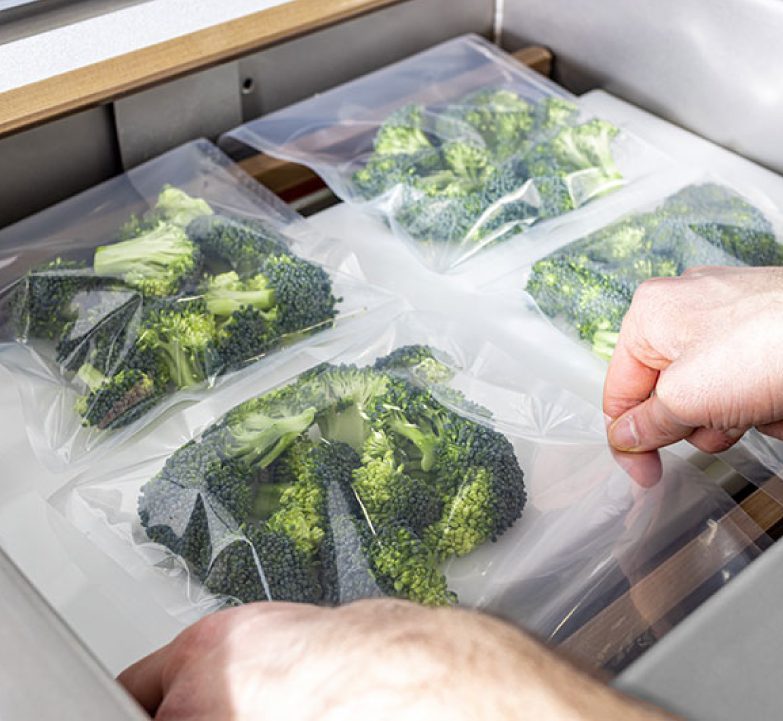
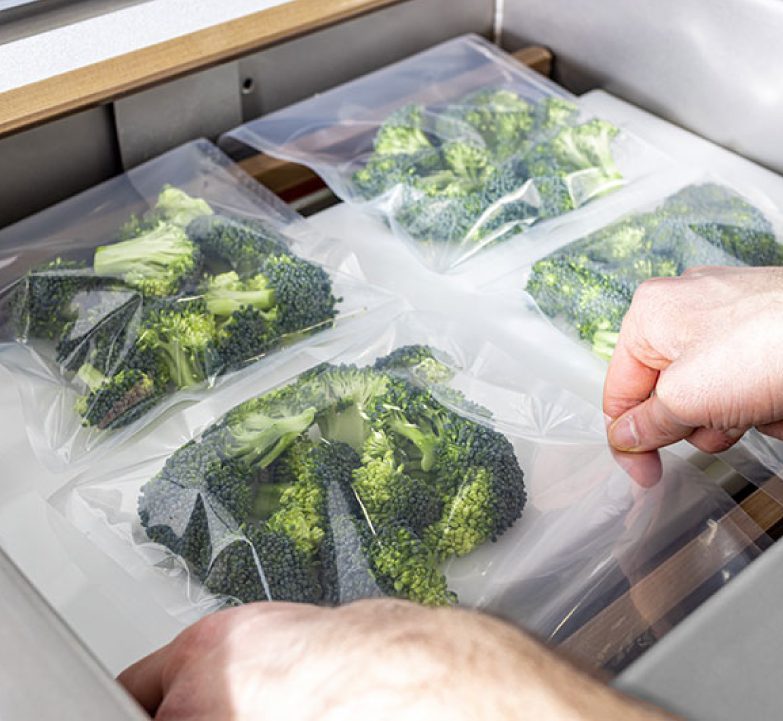
Wrapping up.
Vacuum sealers are an important investment for food packaging businesses. They help to keep products fresh for longer, increasing their shelf life and aid with many recipe creation ideas. However, like any other machine, vacuum sealers can develop issues that need to be addressed. By keeping your machine’s preventative maintenance up to date and troubleshooting common issues with vacuum sealers, you can keep your machine working efficiently and ensure that your products are packaged properly.
Need your chamber vacuum sealer repaired?
Reach out to our service team.
Share this post
Have a project in mind?
Get in touch today for a custom quote.